Spray coater operation
The machine atomises the coating liquid with a spray valve, which is connected to the liquid’s containers. It coats all products on the product holder. The atomised coating is highly flammable, which is why there’s a separate vapour extraction unit at the back of the machine. This unit ensures everything’s sufficiently ventilated. The underside of the products, which shouldn’t be coated, lies protected on the holder. The entire process takes place inside a mobile frame with braked wheels.
The products lie on a removable product holder. Depending on the product size, the machine can coat different quantities in one production run. In this case, we’re talking about 96 products at a time. The machine automatically makes sure that the rings are underneath the spray valve, then performs a single spray pulse for each position. Though there’s no continuous coating spray, the machine does have the capability for it.
Specifications
- Various batch sizes can be realised
- Mobile frame
- Automatic cleaning between production runs using flushing liquid
Get more information
Wondering how the machine could be useful for your organisation? Request more information quickly and easily.
"*" indicates required fields
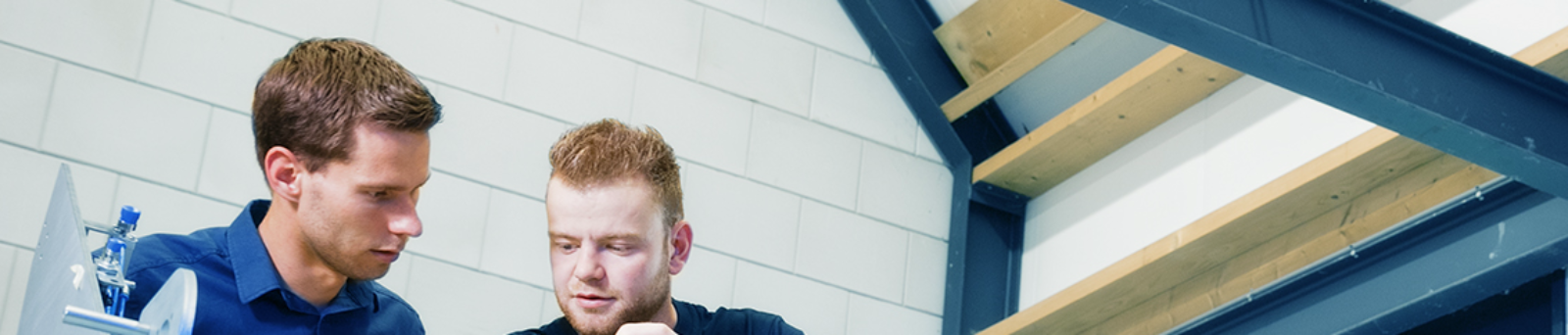
Why choose GTE Engineering?
GTE specialises in designing and producing tailor-made machines for the medical and pharmaceutical industry. Based on your specific needs, we’ll work together on the solutions to the issues you’ve run into.
Curious about what we could do for you?
Let us call you back
Curious about how our machines can be used within your organization? Request more information quickly and easily.
"*" indicates required fields
We are ready to help you!
Mercuriusplein 45971 LW Grubbenvorst (Nederland)
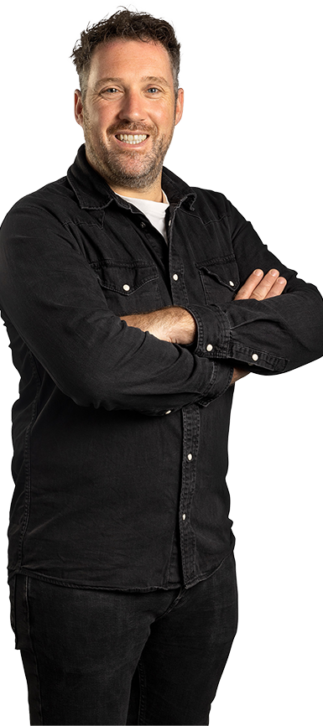
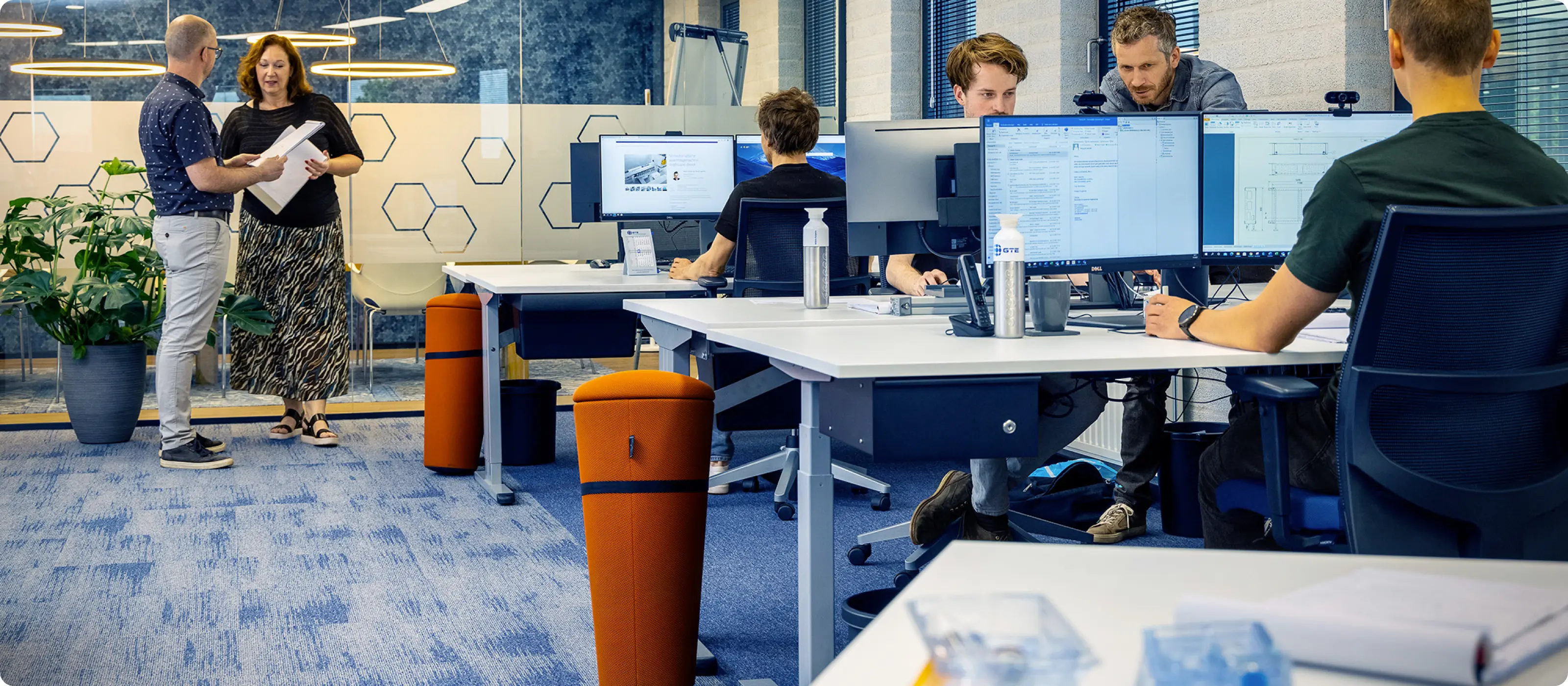