This is how the semi-automatic assembly machine for eye drop devices works
The semi-automatic assembly machine for eye drop devices is a total solution for punching, assembling and packaging an eye drop device. In the first station, the operator punches the molded devices. Then, in the second station, the eye drop tubes are automatically removed from a roll and placed in the devices and checked with a Vision System. In the third station, the devices are packaged.
The operator operates the machine according to a roadmap. The information is logged on a USB stick which can be used to print batch labels.
Specifications
- Consists of three separate stations
- Punching station
- Separating and assembling station
- Folding and packaging station
- Checks through Vision System
- Complete solution for assembling and packaging
- Fully customised designed
Get more information
Wondering how the machine could be useful for your organisation? Request more information quickly and easily.
"*" indicates required fields
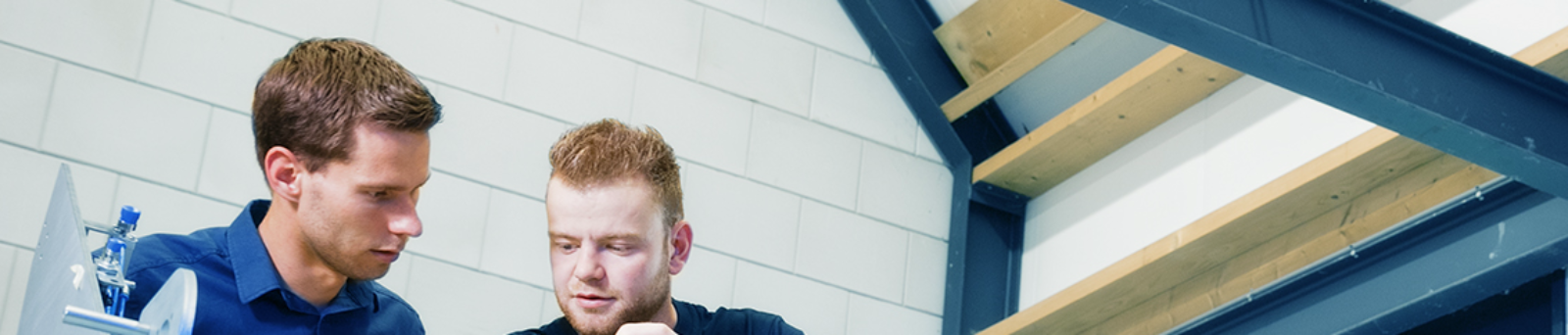
Why choose GTE Engineering?
GTE specialises in designing and producing tailor-made machines for the medical and pharmaceutical industry. Based on your specific needs, we’ll work together on the solutions to the issues you’ve run into.
Curious about what we could do for you?
Let us call you back
Curious about how our solutions can be used within your organization? Request more information quickly and easily.
"*" indicates required fields
We are ready to help you!
Mercuriusplein 45971 LW Grubbenvorst (Nederland)
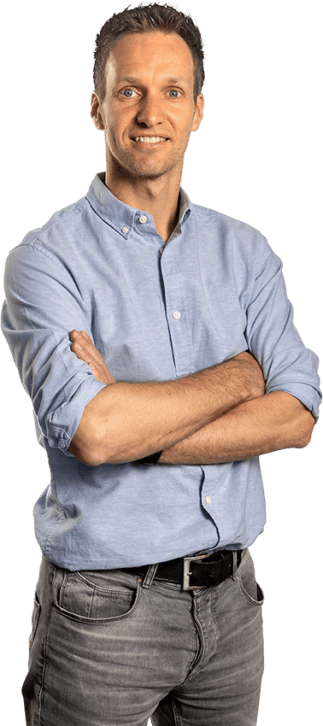
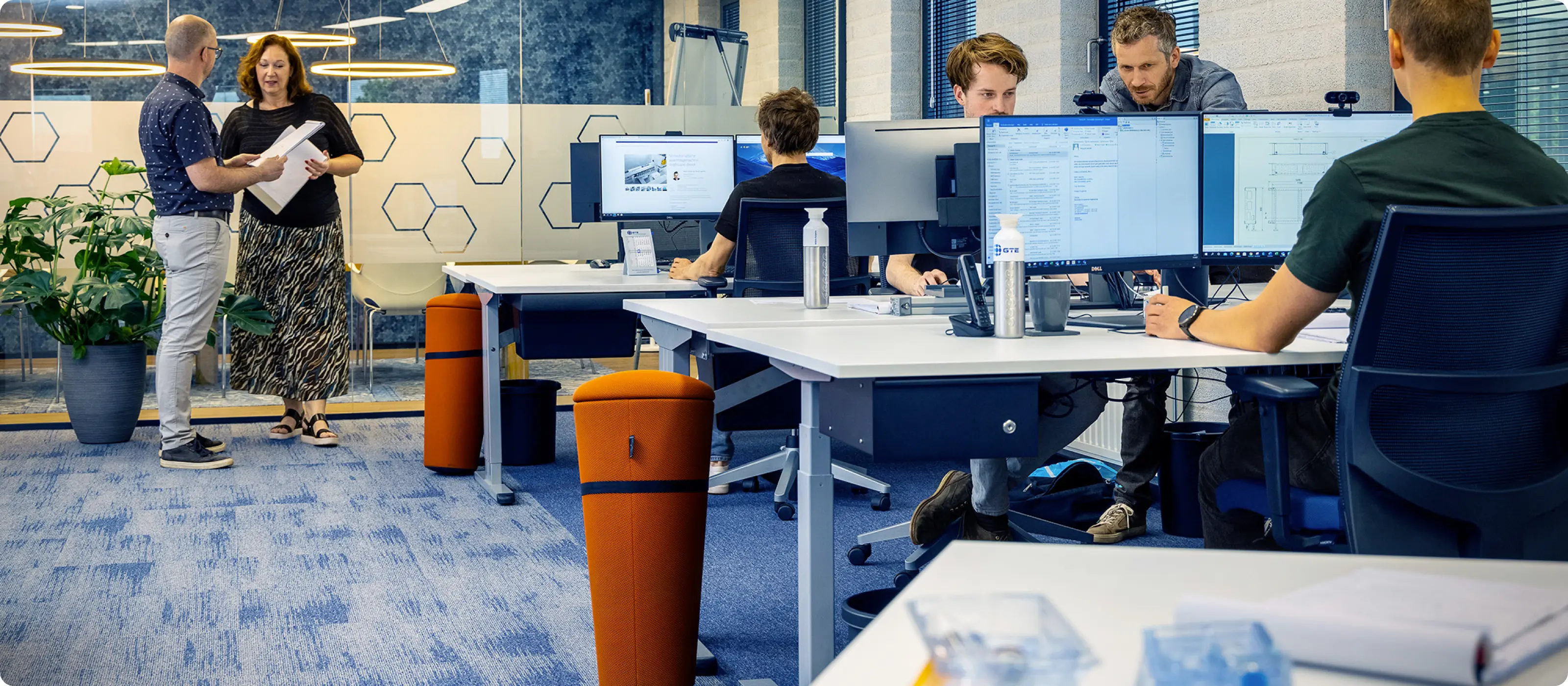