-
Filter on:
- All
- Inspiration
- Knowledge article
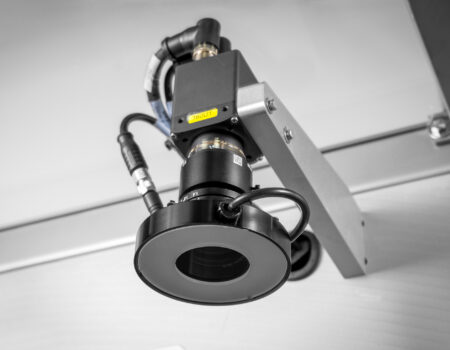
Whitepaper: Everything about vision systems in the pharmaceutical and medical industry
Precision and accuracy are extremely important. Whether they are used for correctly labeling products, or verifying the integrity of packaging, vision systems play a crucial role in any production process. What are their strengths and limitations, how do you prepare for their implementation, and what will the future look like in terms of, for example, AI? We are happy to help you get started; download the free whitepaper!
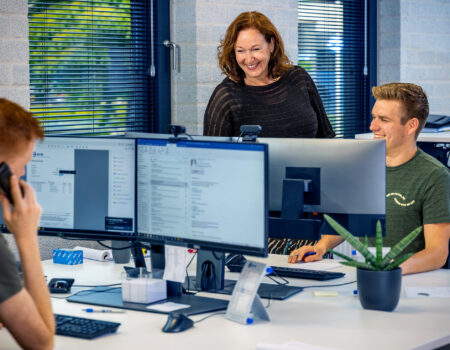
The Importance of IQ, PQ, and OQ in Machine Construction for the Pharmaceutical and Medical Industry
In the pharmaceutical and medical industries, developing machines that meet the highest quality and regulatory standards is essential. Therefore, the steps of IQ (Installation Qualification), PQ (Performance Qualification), and OQ (Operational Qualification) are followed during the construction of these machines. These qualification tests ensure that machines meet the required standards for installation, operation, and performance, and they are a critical part of the validation process.
At GTE Engineering, we use a traceability matrix and provide support with FAT (Factory Acceptance Test) and SAT (Site Acceptance Test) protocols to make the validation process structured and efficient. This approach guarantees that all requirements are documented and that the machines meet the highest standards in the pharmaceutical and medical industries.
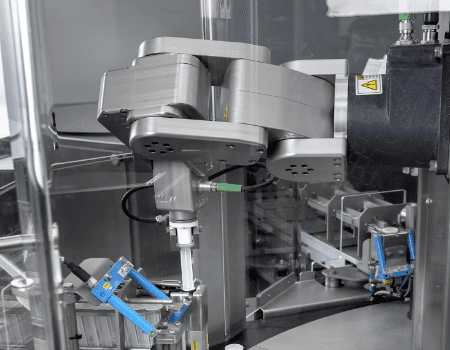
The LAP-C with Mecademic robot
GTE designed and built the LAP-C. A circular platform for assembling and/or packaging medical products. When we design the LAP-C as an assembly machine, we often use a Mecademic robot.
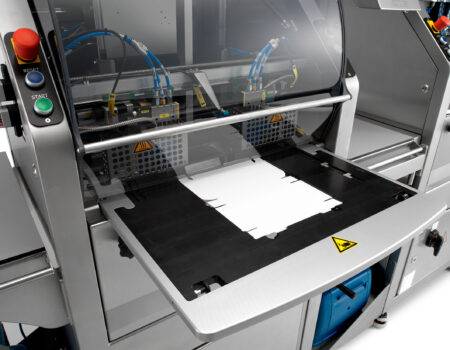
High mix low volume manufacturing
In the pharmaceutical industry, there is a growing demand for high mix low volume manufacturing (HMLV). HMLV signifies that medications and medical devices are increasingly being personalized, tailored more specifically to the patient: a greater variety of medical products combined in smaller quantities.
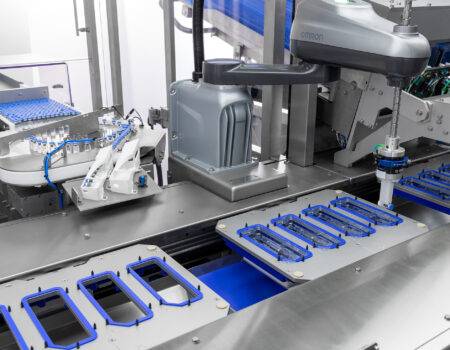
3D printing in engineering– thinking out of the box
Years ago, in 2001, GTE engineering embraced 3D printing for the creation process of its exclusive machines. Until then it was science fiction. Today we can no longer live without it. How do we use 3D printing at GTE and what advantages does it have?
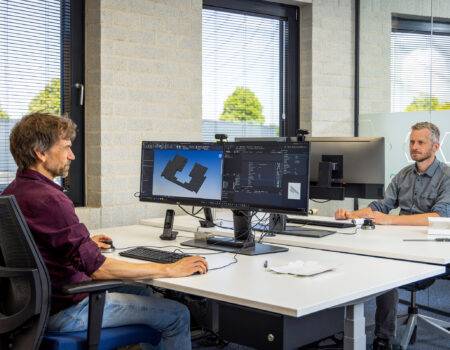
What is ‘Smart Customization’?
ETO, CTO and Smart Customization. Terms that are more often used in mechanical engineering. But what do these terms mean? Everyone working in mechanical engineering should know what development these words describe.
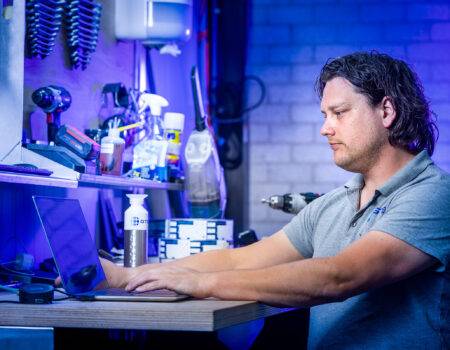
Considerations when selecting reputable machine developers
What factors should you consider when selecting a machine builder? Do they meet the stringent quality standards of the medical industry? While there are numerous legal regulations in place to ensure machine and product quality, it’s crucial that machine designers and builders are cognizant of these requirements. Additionally, take into account three key factors that can impact both the machine and your product’s quality: the human factor, the product design, and the proficiency of the machine builder.
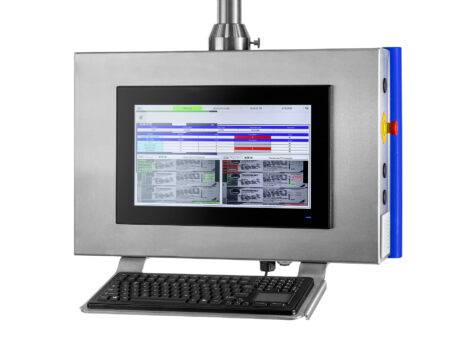
Accepting downtime is a mortal sin!
Everyone knows that companies are all about production, or ‘adding value’. Value is everything the customer needs and pays for. All other activities support this. That’s why it’s so strange that unplanned downtime is so quickly accepted and seen as ‘normal’. Many companies are not aware of how often the production line comes to a standstill. People quickly get used to it and accept downtime on a production or assembly line. However, a production line coming to a standstill is disastrous for the organization. If no value is added, the entire organization comes to a standstill.